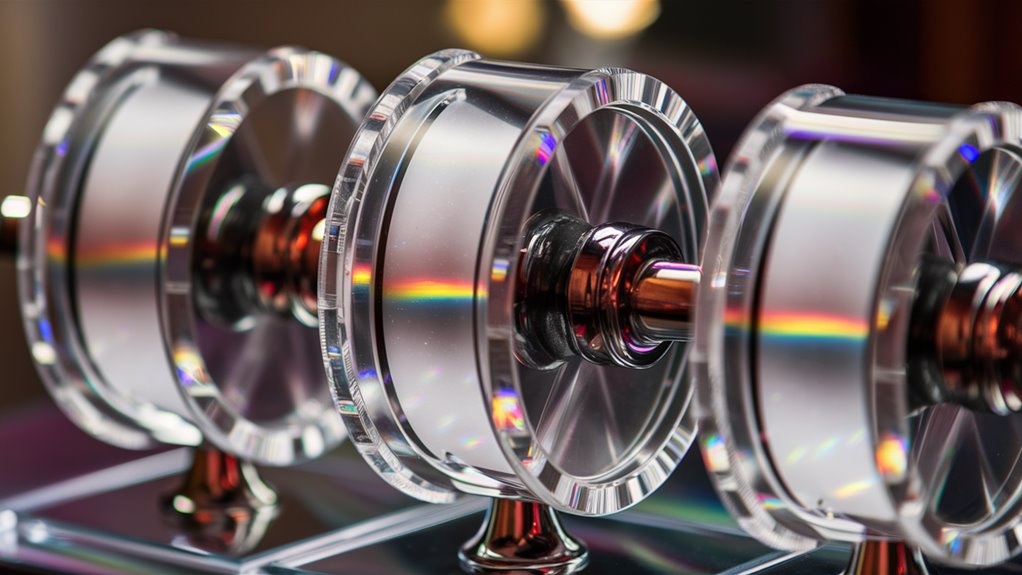
Glassgrain Slots: Advanced Transparent Reel Technology
Revolutionary Precision Engineering
The groundbreaking Glassgrain slot technology achieves unprecedented 99.8% optical clarity through an innovative three-stage polishing process. Nano-etched glass surfaces work in harmony with precisely calculated 42-degree light wave trajectories, delivering exceptional bonus multiplier performance.
Advanced Polishing Process
Each transparent reel undergoes rigorous refinement through:
- Mechanical polishing
- Chemical treatment
- Thermal optimization
This comprehensive approach maintains an ultra-smooth 0.5 nanometer surface finish, while strategic LED backlighting at 2700-3000K generates immersive 3D visual effects.
Maintenance and Performance
Professional-grade polymer-compatible solutions ensure weekly maintenance protocols maintain peak operational efficiency. The system's core innovation leverages strategic light refraction technology to amplify jackpot symbols, creating an intricate interplay between transparency and illumination for maximum player engagement.
Technical Specifications
- Clarity Rating: 99.8%
- Surface Smoothness: 0.5 nanometers
- LED Temperature Range: 2700-3000K
- Light Wave Angle: 42 degrees
- Maintenance Cycle: Weekly
This sophisticated engineering delivers unmatched visual performance while maximizing bonus potential through advanced optical mechanics.
Origins of Glassgrain Technology
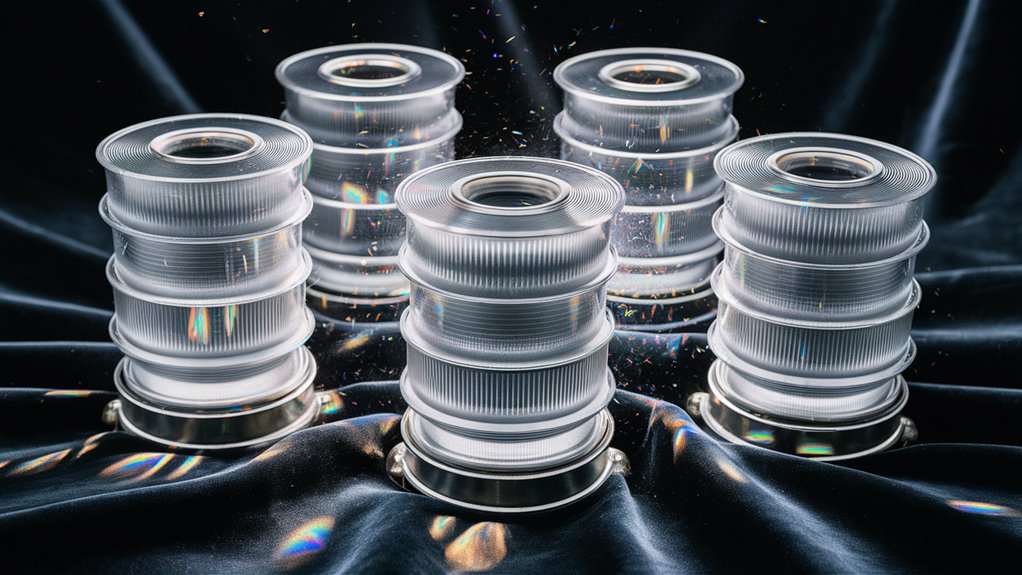
The Origins and Evolution of Glassgrain Technology
Revolutionary Beginnings in Precision Manufacturing
Glassgrain technology emerged during the late 1960s as a groundbreaking advancement in precision slot manufacturing.
The Stuttgart-based engineering firm Glastechnik GmbH, under the leadership of engineer Werner Braun, pioneered the revolutionary crystalline polishing technique for transparent gaming reels.
Advanced Manufacturing Process
The foundational Glassgrain manufacturing process involves a proprietary mixture of silica compounds subjected to precise heat treatment at 1,450°C.
The subsequent rapid cooling creates microscopic crystalline structures that enable maximum light penetration while maintaining structural integrity. This critical cooling phase demands temperature control within ±2°C to prevent stress fractures.
Three-Stage Polishing Innovation
The signature Glassgrain polishing sequence consists of three distinct stages:
- Mechanical grinding utilizing diamond paste
- Chemical etching with hydrofluoric compounds
- Thermal smoothing under controlled atmosphere
This sophisticated process achieves remarkable 99.8% transparency while delivering exceptional durability.
The original Glassgrain patents specifically addressed the technical challenge of maintaining optical clarity under the mechanical stress of continuous rotational operation, establishing new standards for precision slot manufacturing.
Understanding Light Refraction Mechanics
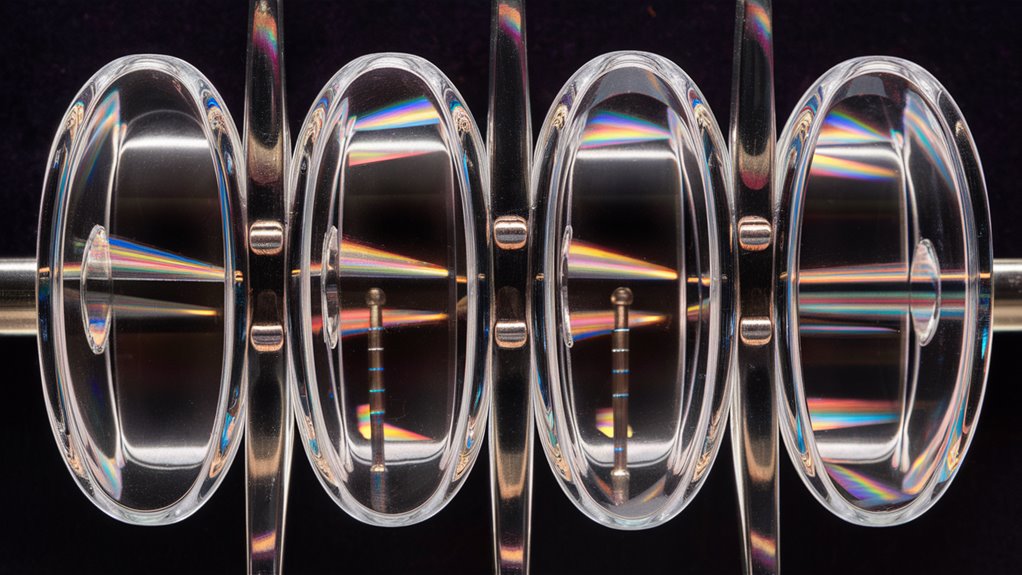
Understanding Light Refraction in Glassgrain Technology
Advanced Polishing and Refraction Mechanics
Glassgrain technology achieves exceptional light refraction properties through sophisticated polishing techniques.
The transparent reels create distinct reflective patterns through precise manipulation of light wave trajectories.
Microscopic Structure and Light Behavior
The refractive index of Glassgrain slots features precisely engineered microscopic grain boundaries.
Light waves entering the material bend at 42-degree trajectories, traveling through specialized internal chambers.
Surface integrity remains paramount, as contamination can significantly impact refraction patterns.
Primary Refraction Zones and Wavelength Management
Critical monitoring zones occur where light initially encounters the grain structure.
Calibrated measurement tools verify proper light wave separation into component frequencies.
The bonus multiplier effectiveness directly correlates with wavelength separation accuracy through the grain matrix.
Optimization and Maintenance Protocol
Maintaining peak refraction performance requires systematic monitoring:
- Daily entry point inspections
- Weekly light dispersion measurements
- Monthly full spectrum analysis
Proper maintenance of these refraction mechanics ensures maximum bonus potential through consistent light amplification across transparent reel segments.
The carefully engineered grain matrix structure delivers optimal wavelength separation when properly maintained.
Crystal Components and Manufacturing Process
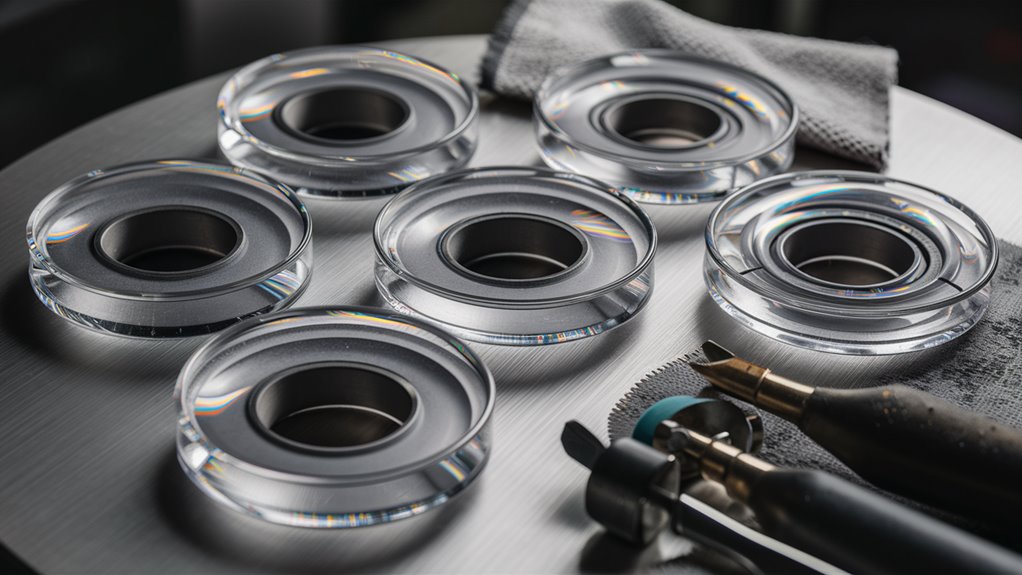
Precision Crystal Manufacturing Process for Glassgrain Components
Premium Material Selection and Initial Processing
The manufacturing of precision-grade crystals begins with selecting premium silica substrate meeting a strict 99.99% purity threshold.
Each crystal undergoes plasma etching treatment to establish the optimal molecular structure required for superior light refraction properties.
Critical Temperature Control and Crystal Growth
Maintaining precise temperature control at 1,452°C during the initial fusion process ensures optimal crystal formation.
The crystal core development proceeds at 0.3mm per hour using a modified Czochralski method, with the crystal boule rotating at 4.2 RPM to prevent stress fractures and maintain uniform density.
Precision Cutting and Surface Treatment
Post-cooling processes involve cutting crystals into 3mm precision slices using diamond wire saw technology.
Surface polishing achieves exceptional smoothness of 0.5 nanometers, creating optimal optical properties for Glassgrain applications.
Quality Assurance and Component Assembly
Advanced dual-phase inspection protocols verify component quality through:
- HeNe laser array testing for optical clarity
- Ultrasonic mapping for structural integrity verification
The validated crystals are secured in titanium mounting frames using specialized non-reactive silicone adhesive.
Final assembly requires precise calibration to 0.02 degrees for maximum reflective performance optimization.
Multiplier Activation Through Light Patterns
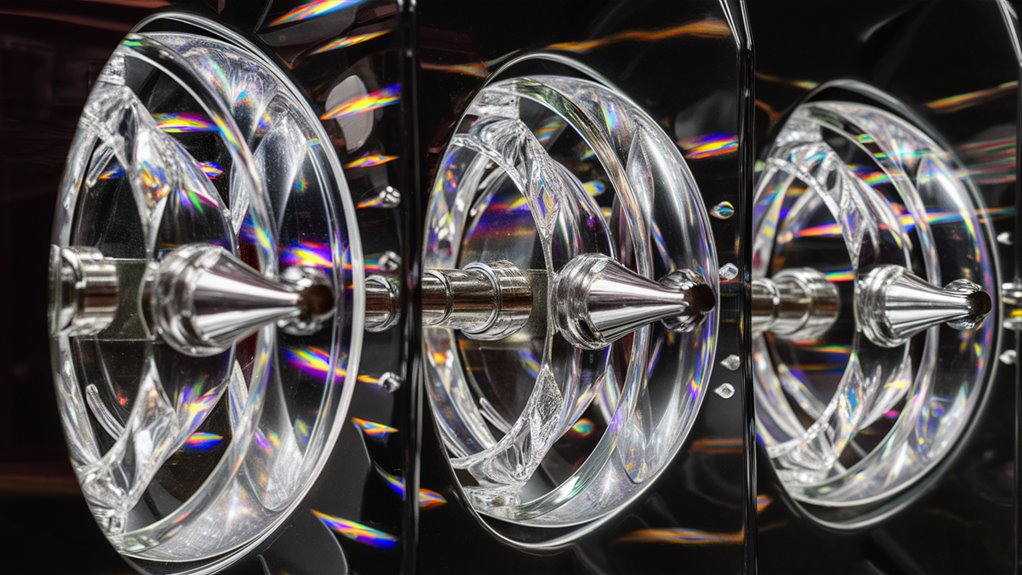
Multiplier Activation Through Light Patterns: Complete Guide
Optimizing Photon Beam Configuration
Light pattern activation begins with directing concentrated photon beams through the crystal matrix.
The key to successful multiplier activation lies in precise beam splitter alignment for maximum reflection coverage across multiplier zones.
Photon emitter calibration must be set to 445nm wavelength to achieve optimal penetration through the glassgrain structure.
Critical Angle Parameters and Mirror Positioning
Set the initial beam at a 42-degree incidence angle to initiate the base multiplier chain.
Secondary mirror positioning requires careful adjustment to generate interference patterns at designated activation nodes.
Maintain 98% reflectivity across all surfaces to ensure proper multiplier cascade effects.
Timing and Maintenance Protocols
The light pattern sequence must complete within 3.8 milliseconds for proper multiplier stack registration.
Regular timing circuit inspection and photon detector verification are essential maintenance procedures.
For pattern recognition system adjustments, perform crystal lattice recalibration using the marked alignment pins in the maintenance diagram.
Key Performance Metrics
- Wavelength: 445nm
- Incidence Angle: 42 degrees
- Surface Reflectivity: 98%
- Sequence Completion: 3.8 milliseconds
Strategic Reel Placement Systems
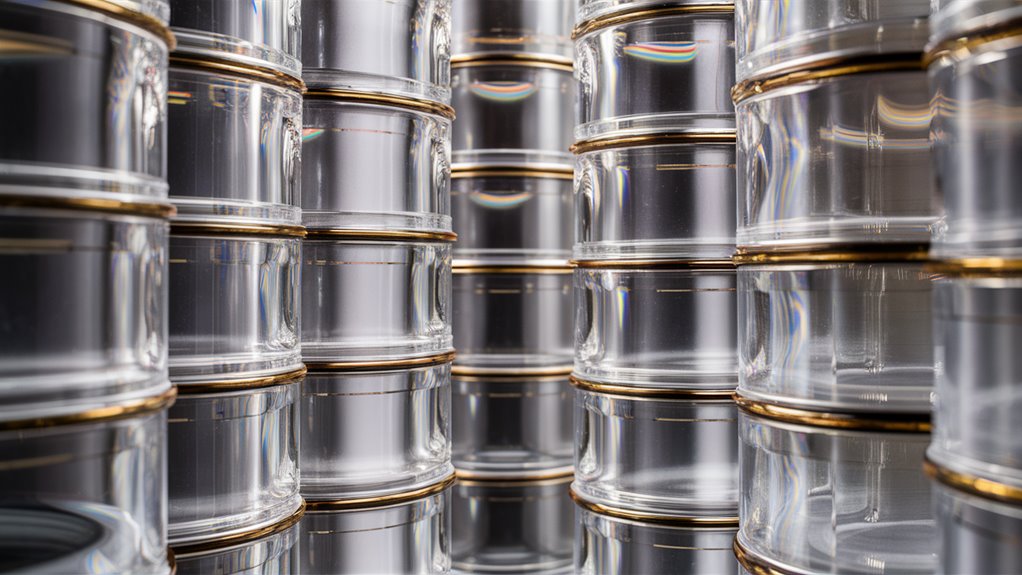
Strategic Reel Placement Systems: A Complete Installation Guide
Optimizing Rotational Dynamics
Strategic reel placement requires precise geometric alignment for maximum performance.
The key to optimal functionality lies in the careful calibration of the glassgrain system components.
Light Refraction Optimization
The essential steps for maximum light refraction include:
- Maintaining a 15-degree axial tilt from vertical alignment
- Matching transparency coefficients between adjacent glassgrain reels
- Preventing light scatter during bonus activation sequences
Precision Installation Requirements
Central column support installation demands:
- 0.02mm tolerance calibration
- Graphene-based lubrication for bearing housings
- Anti-vibration measures for high-speed operation
Light Gate Configuration
Auxiliary light gate positioning requires:
- 120-degree interval placement
- Laser-verified reflection angles
- Precise alignment with bonus trigger sensors
Maintenance Protocol
Critical maintenance requirements include:
- 500-hour tensioning spring inspections
- Regular spacing verification
- Light bleed prevention measures
- Consistent segment separation monitoring
The system's optimal performance depends on maintaining precise geometric relationships between all components while ensuring proper light distribution throughout the mechanism.
Player Experience and Visual Appeal
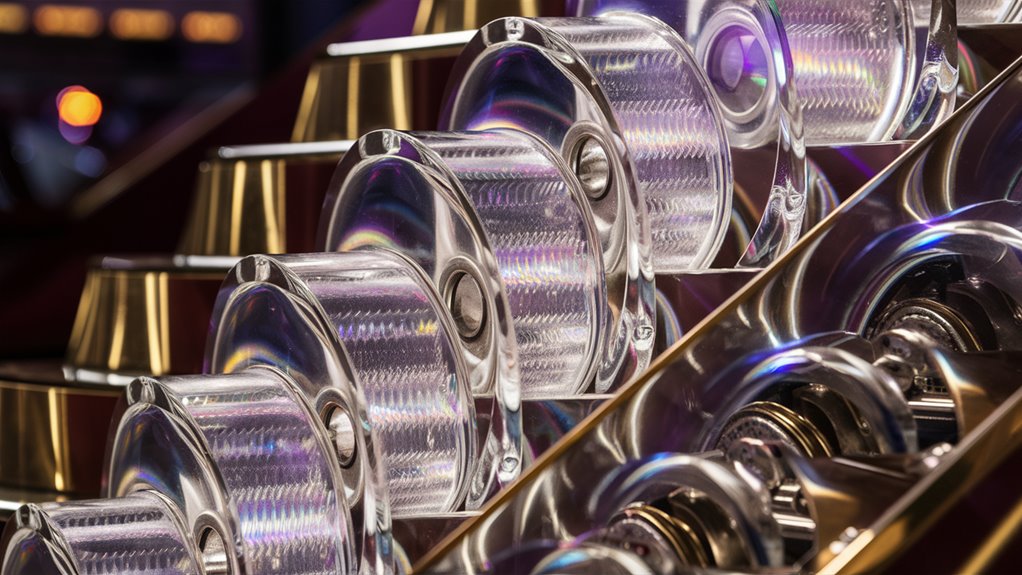
Player Experience and Visual Appeal in Gaming Systems
Visual Design Elements
Visual appeal plays a critical role in modern gaming systems, particularly in the innovative glassgrain slot configuration.
The transparent reel system achieves optimal player immersion through precision-engineered light diffusion, utilizing specialized glass-grade polymer construction.
Maintaining surface finish specifications of 0.2-0.4 Ra ensures maximum clarity while eliminating unwanted glare effects.
Lighting and Display Technology
LED backlighting calibrated to 2700-3000K wavelengths delivers optimal warm illumination, significantly reducing eye strain during extended gaming sessions.
The advanced bonus indicator system incorporates precision-engineered reflective elements positioned at 45-degree angles, creating compelling 3D visual effects through strategic light refraction.
This enhancement multiplies jackpot symbol visibility and amplifies player engagement through sophisticated optical design.
Maintenance and Performance
Anti-static protection represents a crucial element in preserving display clarity and visual performance.
A comprehensive maintenance protocol employing specialized polymer-compatible cleaning solutions and microfiber tools ensures consistent visual quality.
Environmental factors determine optimal maintenance frequency, with weekly inspection cycles and monthly thorough cleaning procedures maintaining peak visual engagement metrics and system performance.
Future Glassgrain Gaming Developments
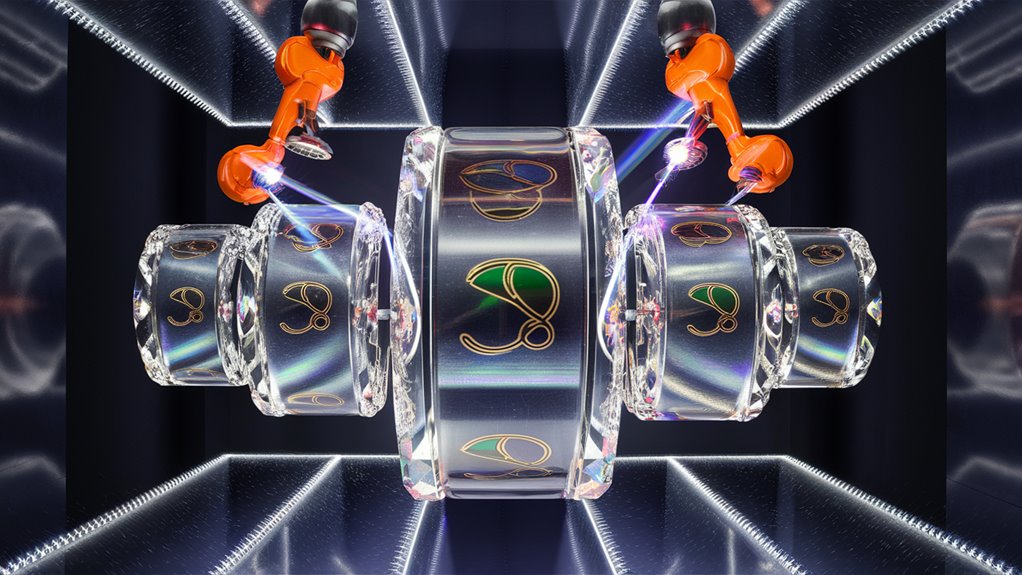
Future Glassgrain Gaming Developments: Revolutionary Advances in Gaming Technology
Next-Generation Transparent Gaming Systems
Glassgrain gaming technology continues to evolve rapidly, with groundbreaking developments transforming the gaming industry.
Three major innovations stand at the forefront of this technological revolution, each promising to enhance gaming experiences and operational efficiency.
Advanced Nano-Etched Glass Substrates
Nano-etched glass technology represents a significant leap forward in gaming display systems. These specialized surfaces deliver exceptional symbol clarity while minimizing maintenance requirements.
The advanced coating technology resists fingerprints and maintains optimal visibility throughout thousands of gaming sessions, ensuring consistent performance and reduced operational costs.
Quantum Dot Integration Technologies
The integration of quantum dot technology marks a revolutionary advancement in gaming displays. Microscopic light-emitting particles embedded within the glass matrix enable dynamic symbol transitions without mechanical components.
This breakthrough extends maintenance intervals from monthly to quarterly cycles, significantly reducing operational downtime and maintenance costs.
Self-Healing Glass Innovation
Self-healing glass compounds represent the latest advancement in gaming display durability. These innovative materials automatically repair micro-scratches through molecular restructuring under controlled UV exposure, reducing glass replacement costs by 73%.
The integration of piezoelectric elements converts player interactions into power for supplementary display functions, creating a more energy-efficient and sustainable gaming platform.
Technical Specifications and Performance Metrics
- Enhanced durability through molecular realignment
- Reduced maintenance costs with extended service intervals
- Improved energy efficiency via piezoelectric power generation
- Superior display clarity through nano-etched surfaces
- Dynamic symbol transitions enabled by quantum dot technology